STRETCH FORMING PRESSES
Macrodyne Stretch Forming Presses are available in a variety of configurations to form Sheet Metal, Extrusions, and Brake-Formed Profile Parts by using the Stretch Forming method. The Sheet Press is typically used to form large sheets, while the Swing Arm (V-Press) is used for Extrusions and Break Formed parts. Each can be equipped to form any of the three types of parts. These forming methods are used worldwide across many industries. Most notable in the Aerospace industry. We understand the aerospace industry’s requirements, and we have consistently delivered solutions to them that are reliable, repeatable, and precise. Macrodyne is committed to supplying quality hydraulic press solutions that exceed the needs of your industry.

SHEET STRETCH FORMING PRESS FOR FUSELAGE SKIN PANELS
Designed to grip each end of the sheet stock material. Then it applies the required tension force to stretch the material beyond its yield point and into its plastic region. It maintains the sheet tension while the sheet is wrapped over the Forming Die. This process creates quality parts with no wrinkles, even stress distribution, and minimum spring back.
The machine’s structural components are designed using FEA, stress relieved, and accurately machined to provide rigid support of the forming process.
The Loading, Unloading, and Forming motions of the press are controlled by a PLC-based CNC control system. An added feature of the control system is the ability to create part forming programs. The programs providesconsistent and repeatable forming cycles for quality parts production. The programs can be saved and reloaded for future use.
Mechanical features specifically tailored to our customer’s needs:
Die table size
Die Table Tilt
Yoke Carriages
Yoke Swing
Rotating Die Table
Jaw Centroid Lift
Jaw Rotation
Jaw Oscillation
Strongbacks for Bullnosing with machines with Curving Jaws
Auxiliary Die Tables
Bulldozer for secondary forming operations
Axillary Curving Jaws
Axillary Extrusion Jaw
Walkway Systems – Interior and Exterior
Die Handling Systems
Complete Hydraulic System – sized for the application
Chiller Cooling Water System – if required
Safety Systems – to protect personnel and equipment.
​
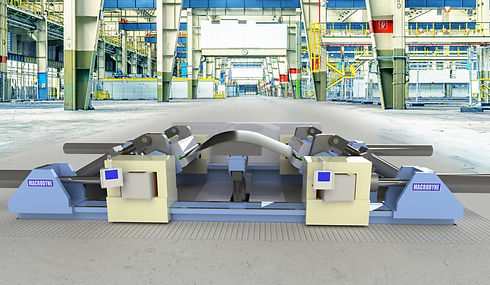
CONTROL FEATURES
PLC-based Control System with HMI for CNC functional axis control for process accuracy, consistency, and repeatability of more than 30 axes of motion. Forming type available based on press type:
Drape
Bullnosing, including Leading Edge Forming
Stretch Wrap – utilizes Tangency tracking device
Stretch Draw
Transverse Forming
Longitudinal Forming
Transverse/Longitudinal – w/ Rotating Die Table
Note: Special part, die, and press forming program development software package available.
V-STYLE STRETCH WRAP FORMING PRESS
Typically used to form small and large Aerospace parts (fuselage frame chords, stringers, longeron, etc.). But often used in other industries that form extrusions or sheet metal brake-formed parts, such as: Rail Car frame components, Industrial Track Rails, Architectural, structural supports, and decorative components, to name a few.
Designed to grip each end of an Extrusion or Brake-Formed sheet metal part with a pair of Jaws. Each Jaw mounts to a tension cylinder that is trunnion mounted to a carriage to allow the Jaw to pivot horizontally. Each carriage is mounted on a Swing Arm. The Swing Arms are pivot mounted on each side of the table. A cylinder drives each Swing Arm to pivot the arms from a position 90 degrees to the table to 10 degrees forward of the table. This arrangement sets the tension cylinders and Jaws parallel to the Die Table mounting surface.
With a forming-die mounted to the Die Table and the part loaded into the Jaws, the press can apply a tension load to the part to stretch the part material beyond its yield point and into its plastic region. It then wraps the part over the die while maintaining the stretching sheet tension. This process evens out the stress distribution in the part cross-section to prevent wrinkling and minimize spring back.
The machines structural components are designed using FEA, stress relieved and accurately machined to provide rigid support of the forming process.
The Loading, Unloading, and Forming motions of the press are controlled by a PLC-based CNC control. An added feature of the control system is the ability to create part-forming programs. Programing provides consistent and repeatable forming cycles for quality parts production. The programs can be saved and reloaded for future use. This reduces setup time for increased efficiency.
MECHANICAL FEATURES SPECIFICALLY TAILORED TO OUR CUSTOMER’S NEEDS:
Tonnage Capacity – 5 to 150 Ton
Die Table Size
Jaw Type
Jaw Rotation
Jaw Lift
Carriage Cross Slide Adjustment
​
​
​
Part Length Capacity
Die Posts
Jogglers w/Jib Crane
Complete Hydraulic System – sized for the application
Chiller Cooling Water System – if required
Safety Systems – to protect personnel and equipment
​
CONTROL FEATURES
​
PLC based Control System with HMI for CNC functional axis control for process accuracy, consistency, and repeatability for up to 30 axes of motion. Controlled forming type available based on press type:
Stretch Wrap Forming
Reverse Bending
Note: Special part, die, and press-forming program development software package available.
QUAD AXIS SWING ARM V-PRESS
The Quad Axis Press is a specialty Swing Arm Press capable of Stretch Forming a 3D part. Six additional axes must be added to each Jaw of the standard Swing Arm V-Press design.
Standard Swing Arm V-Press Axes of Motion – X2 for left and right side
Jaw extend /retract
Jaw horizontal swing
Swing Arm Swing
Quad Axis Swing Arm V-Press Axes of Motion – X2 for left and right side
Standard Axes
Jaw extend /retract – can be carriage motion for some designs
Jaw horizontal swing
Swing Arm Swing
Additional Axes for Quad Axis Press
Jaw rotation – also known as twist
Jaw Lift
Jaw Vertical Swing
The three additional axes of motion to each of the two sets of Jaws, provided the range of motion for true 3D part forming.
This style press could look much different from a typical Swing Arm press due to its configuration. The Jaw extend/retract motions can be controlled by carriage motion. If the carriage height is tall, the carriage and arm configuration can change to support the carriage’s higher loads.